« Une meilleure visibilité à un niveau agrégé, une saturation des capacités de production, avec notamment une allocation dynamique des moules servant à la fabrication en fonction des prévisions de demande, et une amélioration de la qualité de prise de décision ». Voici comment Pascal Gasmeur, Responsable produit chez DynaSys, a mis en avant les bénéfices retirés par son client, le fabricant britannique des conditionnements en plastique rigides RPC, lors d'une conférence sur Supply Chain Event mercredi dernier. Ce grand groupe de 23.000 salariés et 160 sites de production dans le monde a décidé voici trois ans de mettre en place au niveau mondial un processus S&OP standardisé, soutenu par le déploiement d'un logiciel adapté (et non à partir d'Excel comme cela était le cas dans 7 des 20 entités qui utilisaient déjà un processus S&OP). Un processus S&OP standardisé, par famille de produits, à maille mensuelle et sur un horizon d'un an, a été mis en œuvre depuis 2015 sur 25 sites, notamment au Royaume-Uni, en France et en Allemagne. Pour préparer la réunion S&OP multisites, RPC s'appuie sur l'APS de DynaSys, qui permet égalemet de lancer des alertes en cas de problème capacitaire sur un site. CC
Photo : Pascal Gasmeur, Responsable produit
chez DynaSys ©C.Calais
Photo : Pascal Gasmeur, Responsable produit
chez DynaSys ©C.Calais
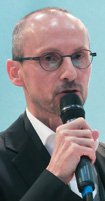