Pour décongestionner son usine de Biessenhofen, Nestlé y a réorganisé son intralogistique en recourant à l’expertise et à des solutions de Still, déployées sans interrompre la production. Une logique en flux poussés impliquait d’encombrant stocks-tampons de matières premières et d’emballages en bord de ligne ; son passage en flux tirés repose sur quatre gerbeurs automatisés EXV iGo pour les acheminer, mais aussi évacuer en retour les matières recyclables et les palettes vides. Dès qu’un besoin est signalé sous SAP par la production, un ordre de transport déclenche le système de convoyeurs reliant l’entrepôt, et ces derniers activent les AGV pour prendre le relais. « Ce transport intelligent s’organise tout seul, sans interface informatique entre la boucle de commande Still et le système hôte Nestlé, déjà complexe. Et les AGV, piétons et chariots élévateurs circulent conjointement sur le parcours sans incident », souligne Bruno Chambraud, responsable du département Intralogistique chez Still France. La réorganisation a aussi regroupé sur un seul magasin une demi-douzaine de stocks existant d’emballages et d’accessoires de production, avec une nouvelle installation équipée d’un rayonnage à accumulation opéré par des navettes Still Pallet Shuttle, la solution allie densité du stock, flexibilité d’utilisation, et sécurité vu que les chariots n’ont plus à s’engager dans des allées. L’usine de Nestlé étant centenaire, Still avait procédé au préalable à une modélisation numérique de l’ensemble du site, ses installations et processus, et évoque un projet « brownfield », plutôt que « greenfield » en partant d’une feuille blanche. MR
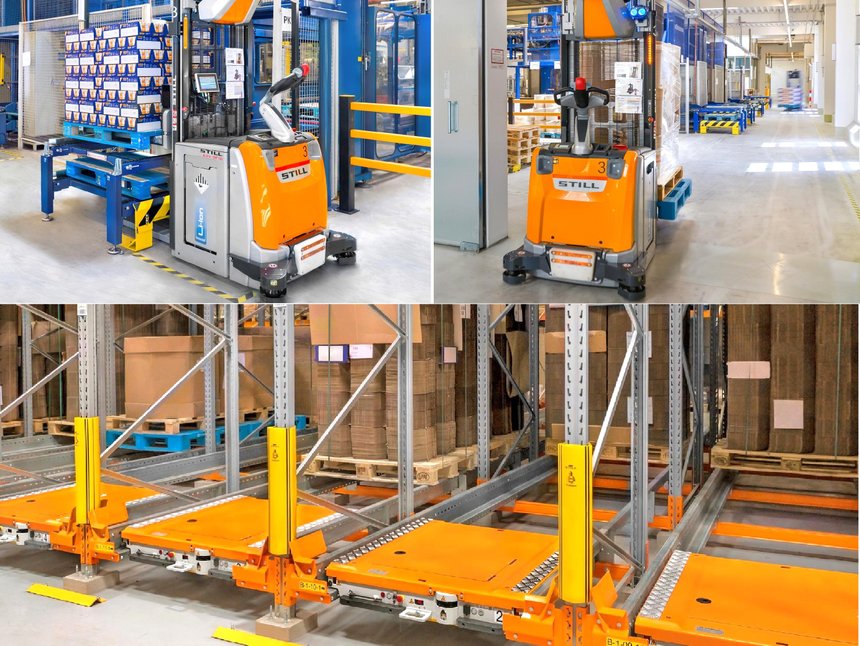
Les AGV Still prennent le relais des convoyeurs palettes pour les acheminements vers les lignes de production, tandis qu’un magasin Pallet Shuttle centralise les emballages. © Still